When it comes to ensuring a seamless installation project, effective coordination and meticulous planning are essential. After securing a transparent bid and assembling the right professional team, the next critical phase is managing the logistics to avoid delays and added costs.
Inventory Parts Up Front
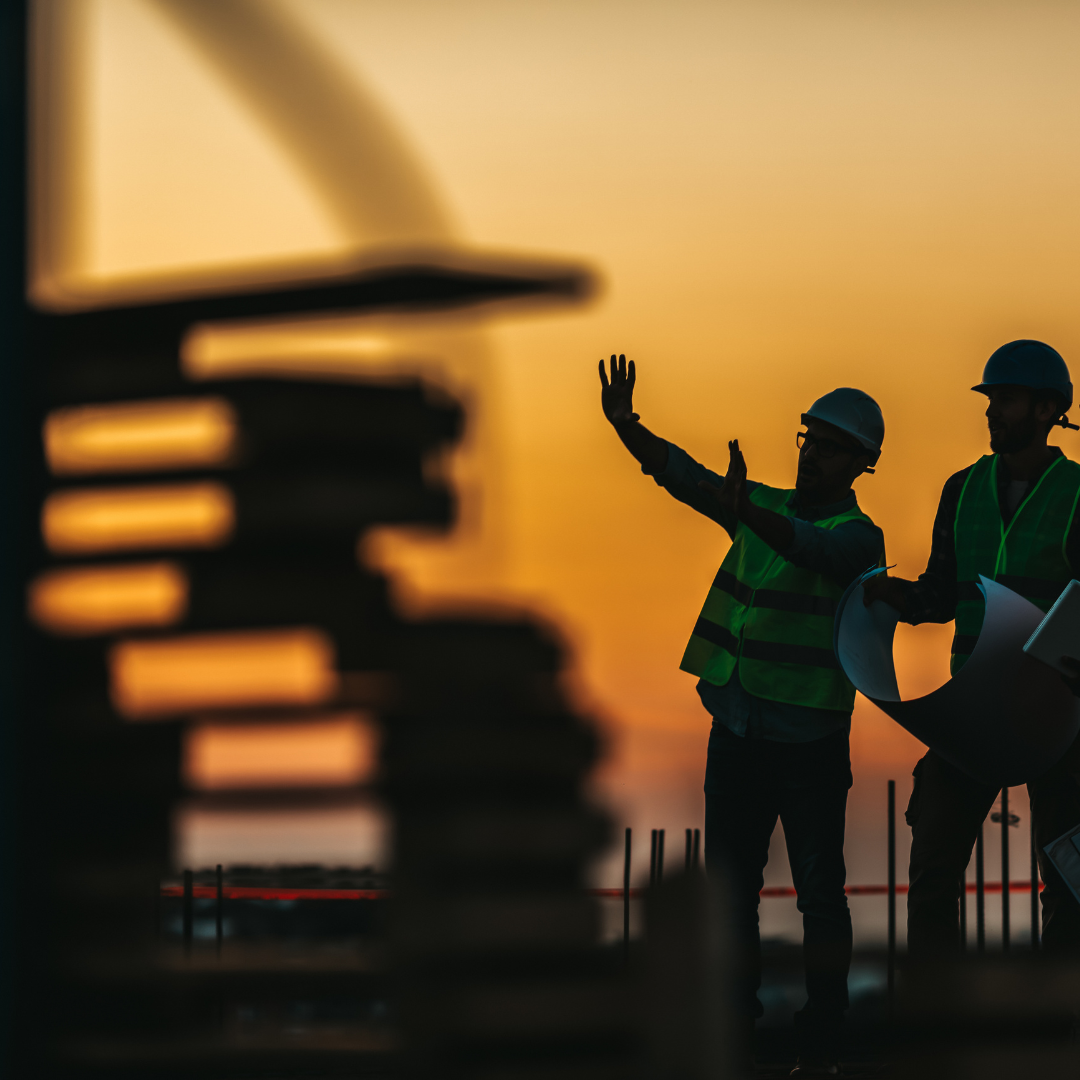
A well-organized inventory process is the cornerstone of a successful installation. Countless stories highlight how poor inventory management leads to inefficiencies, such as installers wasting entire weeks searching for misplaced parts. This not only halts progress but also signals a loss of control over the project.
Failing to inventory materials as they are unloaded carries significant risks:
- Damaged Parts: Identifying and ordering replacements promptly minimizes delays.
- Missing Parts: Discovering shortages early prevents unexpected halts in the installation process.
To mitigate these risks, staging and organizing parts at the outset is critical. For example, scattered pallets can result in time lost searching for components, while unreported damages or losses can lead to expensive delays.
That’s why Ag Installers mobilizes 30 to 60 days before your start date to unload and organize materials systematically. By using a grid system, we track every item pallet by pallet, ensuring efficient storage and the immediate resolution of any missing or damaged items. This meticulous approach ensures the installation process remains on schedule and avoids costly interruptions.
Don’t Leave Anything to Chance
The presence of a knowledgeable and proactive leader on-site is another key to success. Without strong leadership to kick off the installation, valuable time can be lost, and critical issues might go unaddressed, jeopardizing your bird date.
To ensure a smooth start, the Ag Installers team leader conducts a comprehensive site inspection and risk assessment 12 to 16 weeks before your bird date. By proactively addressing potential issues, the team ensures the site is fully prepared for a successful installation. Once on-site, the crew coordinates access, organizes the workspace, and begins pre-assembly using tools like tables, jigs, and shelves. These preparations help streamline the overall process and avoid last-minute challenges.
Planning Ahead Continually
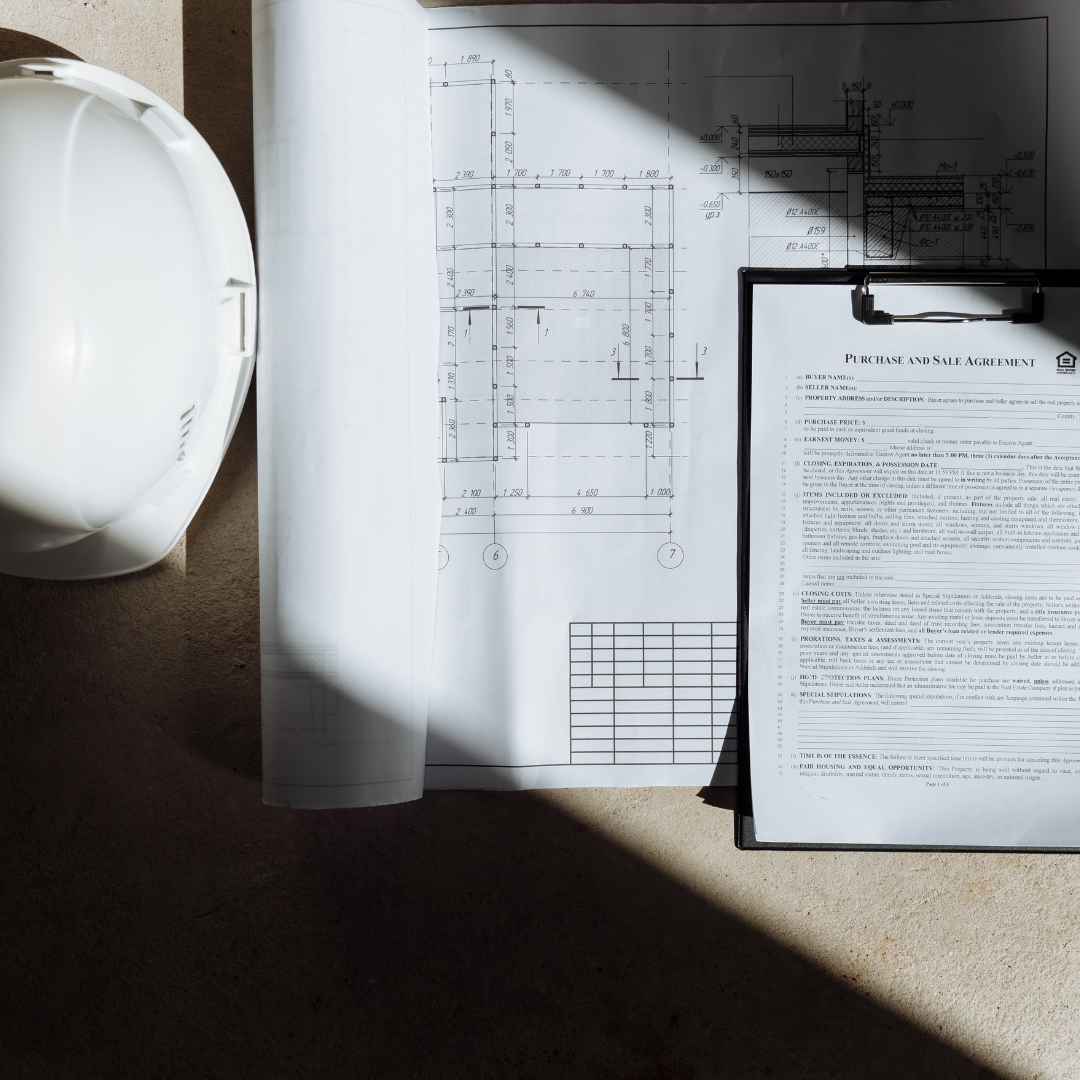
While many installation crews focus solely on day-to-day tasks, this approach often leads to avoidable delays when materials or resources are unexpectedly unavailable.
At Ag Installers, we provide weekly reports with a three-week lookahead. This proactive planning ensures that:
- All parts are on-site.
- Coordination with other trades is seamless, preventing scheduling conflicts.
- The entire project remains on track for timely completion.
By thinking ahead and maintaining open lines of communication, we minimize stress and avoid disruptions to your timeline.
Conclusion
Effective coordination and planning are essential to a stress-free egg equipment installation. By inventorying parts upfront, maintaining strong on-site leadership, and planning ahead, you can ensure your project progresses smoothly and stays within budget. Ag Installers consistently delivers the organization, expertise, and proactive management needed to make your installation a success.
In the coming issues, we will explore more common mistakes to watch for during cage-free installations and provide tips to help you navigate the process smoothly. By staying informed and proactive, you can keep your project on track and meet your bird date with confidence!